Part 1 - PCB Substrates: The Truth About Cost vs Performance in 2025
The Basics of PCB Substrates
PCB substrates serve as the critical foundation for every electronic device you interact with: smartphones that process your daily communications, medical equipment that monitors vital signs, and advanced automotive systems that ensure safe transportation. FR4 continues to dominate the market as the standard substrate material across most industries, priced affordably at $0.10 to $0.50 per square inch. Yet 2025 marks a decisive moment where specialized materials are increasingly essential for performance-critical applications.
Our technical analysis of various PCB substrates reveals how material selection directly shapes device performance parameters and long-term reliability. These materials exhibit dielectric constants ranging from 2.5 to 10.8, a property that directly impacts signal quality in high-frequency circuits. For applications that generate significant heat, ceramic substrates offer exceptional thermal conductivity values of 20-200 W/mK, vastly outperforming FR4's limited capability of 0.3-0.4 W/mK. This superior thermal performance comes at a premium price point, ranging from $2.00 to $10.00 per square inch. Similarly, high-frequency applications often require specialized Rogers materials priced between $5.00 and $20.00 per square inch. These price-performance relationships create a technical puzzle that PCB designers must solve for optimal product outcomes.
-
Watts Per meter-Kelvin (W/m·K): is a measure of how well a material conducts heat.
Dielectric Constant (Dk): Of a PCB substrate is a measure of how much the material slows down an electric field compared to a vacuum, and it directly affects signal speed, impedance, and signal integrity in high-frequency designs.
-
Understanding PCB Substrate Materials
PCB design excellence starts with the substrate, the foundational material that supports all electronic components and conductive pathways. While attention often focuses on visible components and copper traces, the substrate silently dictates your circuit board's electrical, thermal, and mechanical performance capabilities.
What is a PCB Substrate and Why Does It Matter
The PCB substrate functions as the non-conductive base upon which your entire circuit board is built upon. Modern substrates feature a sophisticated "sandwich" structure with distinct functional layers. The central core provides rigid insulation covered with copper foil, establishing structural integrity. A prepreg layer surrounds this core, acting as a binding dielectric material. The outer foil layer creates surfaces where components attach and traces form. A protective solder mask shields copper traces from oxidation damage.
Your substrate selection directly determines three critical board characteristics. First, the substrate's dielectric constant affects signal integrity, particularly in high-frequency applications, where materials with dielectric constants between 3.5 and 5.5 deliver optimal performance. Second, the glass transition temperature (Tg) marks the point at which your substrate shifts from rigid to soft, a key factor in reliability across different operating temperatures. Third, mechanical properties like tensile strength and flex resistance establish physical durability standards.
Common Types of PCB Materials Used Today 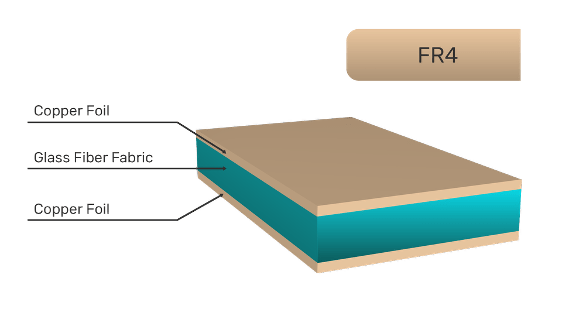
FR-4 dominates today's PCB market as the industry standard. This woven glass material, reinforced with epoxy resin, offers an ideal balance: low cost, good performance, lightweight properties, and effective moisture resistance. However, FR-4 shows limitations through higher dielectric loss, making it unsuitable for high-frequency circuit designs.
Specialized applications demand alternative materials with enhanced capabilities. Polyimide substrates excel when your design faces extreme temperature challenges, featuring a Tg of over 250°C-far beyond that of standard materials. PTFE (Teflon) offers exceptional dielectric properties and frequency stability, making it the preferred choice for RF applications that require precise signals. High-power designs benefit from ceramic-based substrates due to their superior thermal conductivity, which efficiently dissipates heat from power-intensive components.
Rigid vs Flexible Substrates: Key Differences
The fundamental distinction between rigid and flexible PCBs lies in their base materials and resulting physical properties. Rigid PCBs primarily use fiberglass-reinforced materials like FR-4, which maintain their fixed positions, providing excellent mechanical stability and consistent electrical performance. Flexible PCBs use materials like polyimide or polyester that allow for bending, twisting, and folding while maintaining electrical connectivity.
Flexible substrates offer distinct advantages: adaptability to complex three-dimensional shapes, superior resistance to vibration and mechanical shock, and significantly reduced weight and dimensional footprint. These benefits come at higher production costs compared to rigid boards. For advanced applications requiring combined properties, rigid-flex PCBs integrate both rigid and flexible sections within a single board, eliminating connector interfaces between separate boards and enhancing reliability in challenging operational environments.
Cost Breakdown of Different PCB Substrates
PCB designers face a critical balance between performance specifications and budgetary constraints when selecting substrate materials. Cost variations across substrate types substantially impact both initial production investments and the long-term value proposition of finished electronic products.
FR-4: The budget-friendly standard
FR-4 stands as the foundation of modern PCB manufacturing due to its exceptional cost-performance ratio. This flame-retardant glass-reinforced epoxy laminate typically costs between USD 0.10 to USD 0.50 per square inch, establishing the baseline for material cost calculations. FR-4 manufacturing expenses scale predictably with board thickness, enabling precise project budgeting. Engineers requiring enhanced thermal stability can specify high-grade FR-4 variants with elevated temperature resistance (TG 130-140), available at a modest cost increase while maintaining manufacturing compatibility with standard processes.
When and Why CEM or PET Might Be Cheaper
Image Credit: Venture Electronics - CEM 1 PCB: The Ultimate FAQ Guide
Composite epoxy materials offer strategic cost advantages in specific design scenarios. CEM-1 combines paper core with dual layers of woven glass epoxy, priced below standard FR-4 but functionally limited to single-sided applications. CEM-3 delivers savings of USD 1.00 to USD 2.00 per square meter compared to FR-4, while supporting double-sided designs with plated through-holes, making it ideal for cost-sensitive consumer electronics.
Polyethylene terephthalate (PET) substrates present compelling economics for flexible circuit applications. These materials offer excellent moisture and chemical resistance, alongside mechanical flexibility. However, their 80°C glass transition temperature creates processing limitations that prevent the use of standard soldering techniques. This temperature constraint positions PET primarily within disposable electronics and low-cost consumer products where assembly alternatives to soldering can be implemented.
How Much Do High-Performance Materials Like Rogers or Ceramic Cost?
Image Credit: Hemeixin - RF PCB Design and Manufacturing | High Frequency PCB & Microwave PCB
The financial step-up to high-performance substrates represents a significant design consideration. Rogers materials command USD 20.00 to USD 75.00 per square inch-approximately 40-150 times the cost of basic FR-4. Similarly, ceramic substrates range from USD 2.00 to USD 10.00 per square inch, with pricing directly correlated to their superior thermal and electrical specifications.
Despite their premium positioning, these advanced materials deliver essential capabilities that justify the investment in specialized applications. Rogers materials strategically position between conventional laminates and premium ceramics, offering optimized electrical performance with manageable fabrication costs. This technical value proposition proves particularly compelling for infrastructure, aerospace, and defense applications where FR-4's limitations would compromise system performance and reliability.
Conclusion: Choosing Wisely for Performance and Cost
As we've seen, PCB substrate is a foundational choice that impacts everything from signal fidelity and thermal stability to long-term reliability and product cost. While FR-4 continues to dominate for general-purpose designs, today's performance-driven applications often demand advanced materials like Rogers, ceramics, or polyimide. Navigating this landscape requires understanding both the technical specs and the cost trade-offs that define your design boundaries.
In Part 2 , we shift our focus from pricing and material types to performance-critical characteristics that drive real-world design decisions. We'll explore how electrical, thermal, and mechanical properties determine the reliability and suitability of each substrate, empowering you to make informed material choices based on your application's demands .